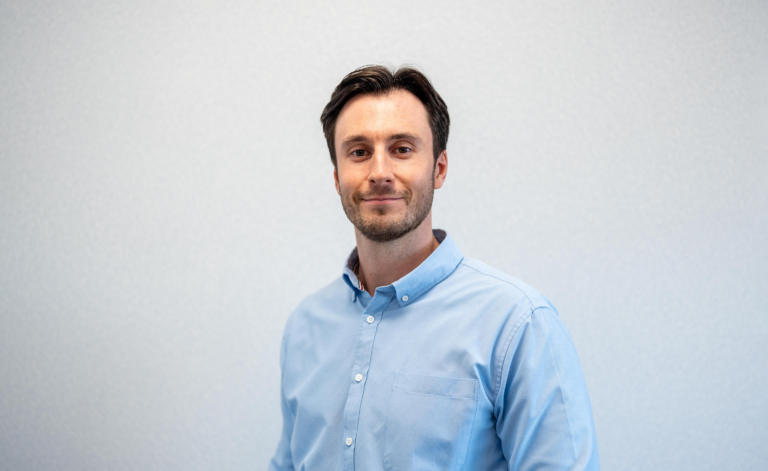
Please describe your role
As Quality Assurance Manager, I’m responsible for all QA activities at Contamac. I have a great team comprising of our Quality Engineer, QA Technician and QA Administrator, and together we look after the Quality Management System; conducting root cause analysis, implementing corrective and preventive action, carrying out internal audits, hosting notified body and customer audits and supporting customers with various requests.
We take a risk-based approach to supplier management to ensure quality throughout the supply chain and we make use of SAP throughout the production process to ensure traceability and as a means of controlling product disposition so that only approved batches are released to the customer. We also manage the calibration and validation activities.
What is your professional history?
After completing my degree in Biomedical Sciences, I began my professional career working for a large manufacturer of construction materials. During my time there, I worked in various positions, starting out as a QA Technician, then spending some time as a Production Area Leader before becoming the Quality Assistant Manager and finally Quality Manager. After seven years, I decided that it was time to apply my skills and experience in Quality management to a role more closely linked to my degree, so in January 2023, I joined Contamac.
Despite the clear differences between construction materials and contact lens materials, it was not difficult to adapt from one to the other, having previously been responsible for Quality at an ISO 9001 certified manufacturing facility within a highly regulated industry. The transition was also helped by the close support of our excellent technical experts at Contamac. I have also been fortunate to undertake further training such as ISO 13585 Lead Auditor and EU MDR Practitioner.
Why is quality assurance so important in the ophthalmic industry?
Quality Assurance is important in any industry, but it is particularly important in the ophthalmic industry. Our customers require materials that are consistently within specification with minimal variation which can be used easily in their own process and produce as few rejects as possible, whilst patients require a material which is safe and effective. To achieve this, we maintain a Quality Management System which encompasses all aspects of the business from procurement of raw materials to dispatch of the finished product, and ensures that our processes are well controlled, and that risk has been considered and mitigated at each stage.
Without effective Quality Assurance, we risk not only causing problems for our customers but also patient safety.
How do you stay updated on the continuously changing regulatory landscape?
There are a number of channels through which changes to the regulatory landscape are made apparent. We hold regular sessions with our regulatory consultants, which keep us updated with MDR and FDA requirements, in particular. Communications are also received from associations and federations such as the European Federation of Contact Lens and IOL Industries (EFCLIN). As for the wider Quality landscape, the Chartered Quality Institute provides a great resource for staying up to date.
How do you think the field of quality assurance will evolve in the future?
In the wider world of Quality, we will see systems become more digitalised and automated – eQMSs are already commonplace but I can see these advancing far beyond where they are now, and I’m sure AI will play a part.
For us at Contamac, as regulatory requirements are becoming more and more stringent, it is clear that being able to demonstrate control throughout the supply chain, from raw materials to end user, is becoming ever more important. With this in mind, good supplier relationships are only going to become more critical as manufacturers will be more and more reliant on documentation throughout their supply chain as evidence of compliance.
What do you enjoy most about working at Contamac and in our industry?
Before I even joined Contamac, when I came in for my interview, Rob McGregor, our Managing Director, was willing to give up the best part of his afternoon to show me around the facilities and explain the processes. This made it very clear to me early on that Contamac is a company that really cares and strives to be world-class in all aspects.
There is a really great team of people at Contamac, and everyone is willing to lend their expertise to help progress through the various projects and day-to-day challenges. As for the wider industry, it’s clearly a close-knit one and it feels great knowing that together we’re improving the wellbeing of millions of people by helping them to see.
How do you and your team support our customers?
As alluded to in the previous question, our customers’ regulatory requirements are only becoming more stringent. The QA department supports customers by helping with enquiries, coordinating with technical quality agreements, completing supplier questionnaires and supporting with other supplier management activities which the customer is required to complete, e.g. by hosting onsite audits.
Working with our internal technical experts and our external consultants to benchmark what we do against MDR and FDA regulatory requirements, a substantial volume of reports have now been compiled in our material technical files which our customers draw upon in order to support their own regulatory requirements.
To help bridge the gap between QA/Regulatory and Commercial, we work closely with our Business Development and Project Manager, Martyn Lewis. Martyn is primarily within the commercial team, but given the regulatory changes our industry has experienced globally in recent years, his role has evolved to support the activities of our QA department and to ensure close communication and partnership throughout. You can read more about Martyn here.
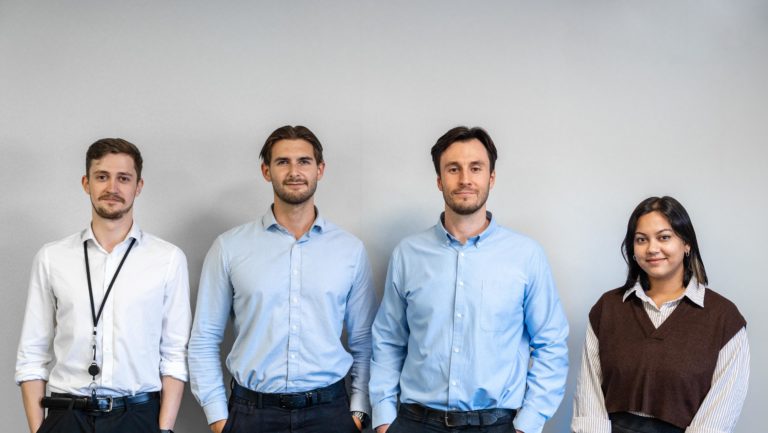
What do you like doing outside of work?
I enjoy music, both listening and playing, having started playing guitar when I was 11. I played in a few bands at school, but now I’m more of a casual player, meeting up with friends to jam every now and then. I also really enjoy going to gigs.
Besides music, I enjoy riding my motorbike (weather permitting!) and I am a regular gym-goer.
If you were shipwrecked on a deserted island, but all your human needs - such as food and water - were taken care of, what two items would you want to have with you?
I’m sure I’d be well entertained exploring and pretending I’m Bear Grylls, so the first thing would be sunscreen as I burn very easily. I’d also bring something to start a big smoky fire in the hope of being discovered.
If you could eat one meal for the rest of your life, what would it be?
I’m not a particularly fussy eater but if I had to pick one meal, it would probably be a traditional roast dinner – I think this would cover most macro and micro nutritional needs, whilst being delicious.